Imagine an implant designed to seamlessly integrate with your unique anatomy. This isn’t science fiction – it’s the reality of 3D printing in healthcare. By enabling the creation of customized 3D printed implants, 3D printing technology is revolutionizing surgery and offering patients a new level of personalized care. Customized 3D printed implants ensure a perfect fit, improving recovery times and overall patient satisfaction.
The landscape of medical implants has undergone a significant transformation with the advent of 3D printing technology. Traditional implants, often made from standardized materials and shapes, do not consider the unique anatomical features of each patient. In contrast, 3D printed implants are tailored specifically to the individual needs of patients, creating a more precise fit and potentially improving outcomes. This customization is made possible by advancements in computer-aided design (CAD) and 3D printing techniques, which allow for the creation of models that mirror the patient’s unique anatomy.
The landscape of medical implants has undergone a significant transformation with the advent of 3D printing technology. Traditional implants, often made from standardized materials and shapes, do not consider the unique anatomical features of each patient. In contrast, customized 3D printed implants are tailored specifically to the individual needs of patients, creating a more precise fit and potentially improving outcomes. This customization is made possible by advancements in computer-aided design (CAD) and 3D printing techniques, which allow for the creation of models that mirror the patient’s unique anatomy. By using customized 3D printed implants, surgeons can enhance surgical precision and patient care.
The process begins with imaging studies, such as CT scans or MRI, which capture detailed information about the patient’s body. This data is then transformed into a digital model using sophisticated software. Once the model is created, it can be modified to enhance fit and functionality, addressing specific considerations such as strength, flexibility, and any pre-existing medical conditions. The use of customized 3D printed implants enables complex geometries and structures that would be difficult, if not impossible, to achieve with traditional manufacturing techniques.
Technological advancements in materials science significantly contribute to the viability of customized 3D printed implants. Modern biomaterials used in 3D printing are biocompatible, meaning they can integrate seamlessly with human tissue, reducing the risk of rejection and complications. Furthermore, processes such as additive manufacturing have led to the development of porous structures that encourage bone growth and promote better integration with the body. The use of customized 3D printed implants is revolutionizing how we approach patient care.
As healthcare continues to embrace innovation, the advantages of customized 3D printed implants are becoming more prominent. By providing tailored solutions that prioritize the individual patient’s anatomy, customized 3D printed implants not only enhance surgical outcomes but also have the potential to improve the overall quality of care in modern medicine.
The process begins with imaging studies, such as CT scans or MRI, which capture detailed information about the patient’s body. This data is then transformed into a digital model using sophisticated software. Once the model is created, it can be modified to enhance fit and functionality, addressing specific considerations such as strength, flexibility, and any pre-existing medical conditions. The use of 3D printing enables complex geometries and structures that would be difficult, if not impossible, to achieve with traditional manufacturing techniques.
Technological advancements in materials science significantly contribute to the viability of customized implants. Modern biomaterials used in 3D printing are biocompatible, meaning they can integrate seamlessly with human tissue, reducing the risk of rejection and complications. Furthermore, processes such as additive manufacturing have led to the development of porous structures that encourage bone growth and promote better integration with the body.
Imagine, quite simply, an implant customized to fit your anatomy. No more science fiction; it is the realization of customized 3D printed implants in healthcare. Customized 3D printed implants change the game: one can create patient-specific implants through 3D printing, giving a new dimension to surgery and a bit of personalized gift to patients.
As healthcare continues to embrace innovation, the advantages of 3D printed implants are becoming more prominent. By providing tailored solutions that prioritize the individual patient’s anatomy, these implants not only enhance surgical outcomes but also have the potential to improve the overall quality of care in modern medicine.
Table of Contents
One-Size-Doesn’t-Fit-All: The Shortcomings of Traditional Implants
Imagine, quite simply, an implant customized to fit your anatomy. No more science fiction; it is the realization of customized 3D printed implants in healthcare. This changes the game: one can create patient-specific implants through 3D printing, giving a new dimension to surgery and a bit of personalized gift to patients.
Weakness of traditional implants: Implants come in standard sizes.
Customized 3D printed implants represent a significant advancement in the field of medical prosthetics and surgical interventions. Unlike traditional implants, which are standardized and may not fit the specific anatomical requirements of an individual, customized 3D printed implants are tailored to match the unique physiological characteristics of each patient.
Once the imaging data is acquired, it is utilized within computer-aided design (CAD) software. This technology empowers healthcare professionals to create highly personalized models that replicate the unique contours and dimensions of the patient’s anatomy. The CAD process not only enhances the design of customized 3D printed implants but also ensures a perfect fit.
The combination of detailed imaging and advanced CAD technology ensures that the resulting customized 3D printed implants are accurate reflections of the patient’s anatomy designed to perform optimally in their specific physiological environment.
Poor Fit: Off-the-shelf implants do not often fit the anatomy of the patient, causing discomfort and instability, in addition to sometimes even prompting an implant rejection.
Limited Functionality: The off-the-shelf implant may not be able to restore proper range of motion or even proper function within the patient and thereby affect quality of life.
Complex Surgeries: Standardized implants force surgeons to alter procedures, which also may increase surgical time as well as potential risks.
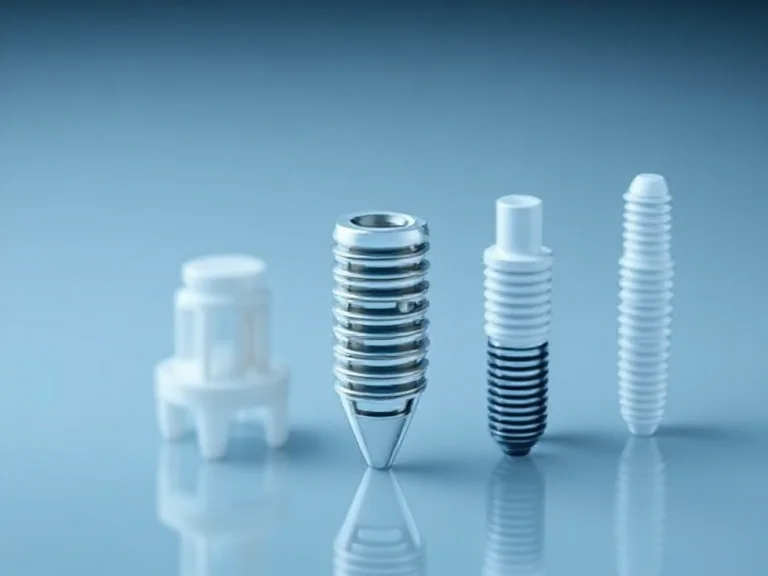
Understanding Customized Implants
Customized implants represent a significant advancement in the field of medical prosthetics and surgical interventions. Unlike traditional implants, which are standardized and may not fit the specific anatomical requirements of an individual, customized implants are tailored to match the unique physiological characteristics of each patient. This precise fitting can have profound implications for both the efficacy of the implant and the overall outcome of the surgical procedure.
The creation of a customized implant typically begins with a comprehensive patient assessment. This assessment is crucial as it provides vital information regarding the individual’s specific needs, health conditions, and anatomical structure. Various imaging techniques are employed during this stage to obtain detailed representations of the patient’s anatomy. Among these, CT scans are particularly noteworthy for their ability to produce high-resolution, three-dimensional images that allow for a thorough examination of complex structures.
Once the imaging data is acquired, it is utilized within computer-aided design (CAD) software. This technology empowers healthcare professionals to create highly personalized models that replicate the unique contours and dimensions of the patient’s anatomy. The CAD process is not merely about scaling standard designs but involves intricate adjustments that ensure a perfect fit. Each customized model is meticulously developed, integrating biomaterials that are compatible with the patient’s body, promoting both functionality and biocompatibility.
The combination of detailed imaging and advanced CAD technology ensures that the resulting customized implant is not only an accurate reflection of the patient’s anatomy but is also designed to perform optimally in their specific physiological environment. Enhanced comfort and function are a direct result of this personalized approach, making customized implants a preferred choice in many medical situations.
The significance of a precise fit in customized 3D printed implants cannot be overstated, particularly when considering customized 3D printed implants. Enhanced comfort and function are a direct result of this personalized approach, making customized 3D printed implants a preferred choice in many medical situations.
3D Printing: Ushering in a New Era of Patient-Specific Implants
3D printing offers a groundbreaking solution:
Customization: Using the medical imaging data such as CT scans, the extremely accurate 3D model of the patient’s bone is developed. Such a model then becomes the template for the perfectly matched implant.
Improved Fit and Function: Custom implants integrate ideally with anatomy of a patient, thereby maximally ensuring stability, comfort, and range of motion. It may even make it speedier to return to normalcy and maybe the quality of life better.
Reduced Surgical Time and Risk: The preformed implants tend to reduce the extent of intraoperative manipulations. Potentially, this could result in short surgeries with rapid recovery.
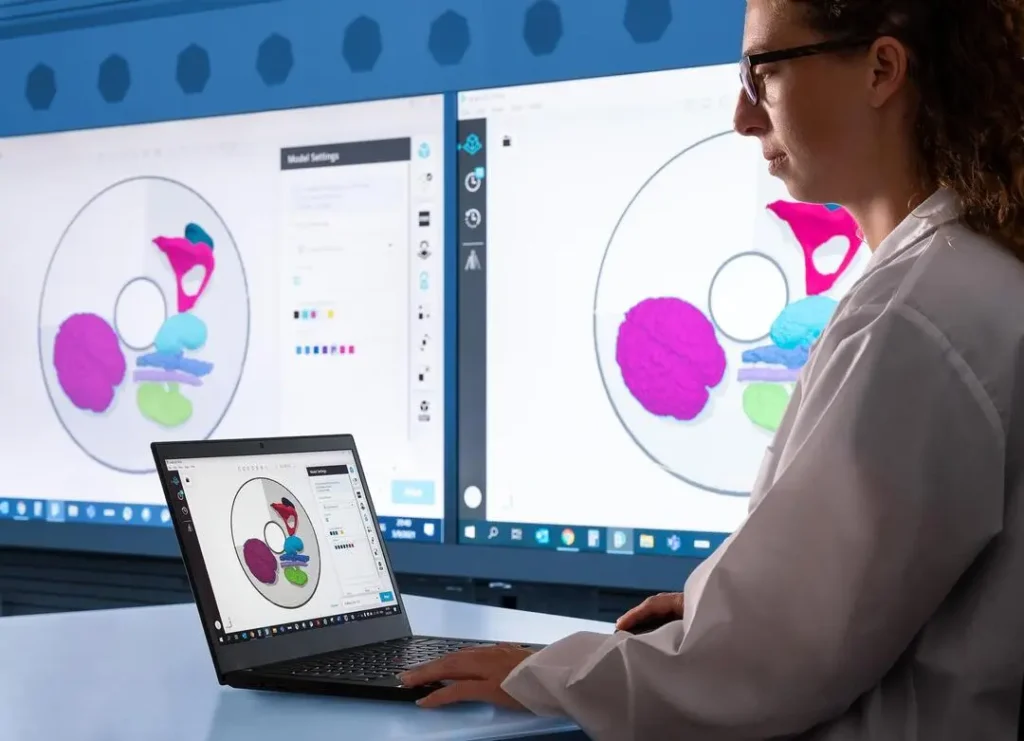
The Benefits of Precision Fit
The significance of a precise fit in implants cannot be overstated, particularly when considering customized 3D printed implants. The integration of advanced technology allows for the creation of implants that are specifically tailored to the unique anatomy of each patient. This personalized approach yields numerous advantages that substantially enhance the surgical experience and ultimate results.
One of the primary benefits of a precision fit is enhanced comfort. Implants that align seamlessly with the patient’s anatomical structure minimize any potential irritation or discomfort post-surgery. Such a tailored fit enables the body to adapt more comfortably to the foreign object, which can lead to higher patient satisfaction levels. In contrast, ill-fitting implants often cause pain and may necessitate additional revisions, underscoring the value of precision in implant design.
Moreover, customized implants contribute to reduced recovery time. When an implant fits accurately, the surrounding tissues experience less trauma during the surgical process. This gentle handling of tissues can streamline recovery periods, allowing patients to resume their normal activities more quickly. Additionally, a precise fit can lead to improved functional outcomes, ensuring that the implant performs as intended and that the patient can regain full mobility and quality of life sooner.
The compatibility between a 3D printed implant and the patient’s anatomy also plays a critical role in minimizing the risk of complications. A well-fitting implant mitigates the chances of dislocation or implant failure, both of which can lead to serious health issues. Overall, the benefits of precision fit in customized implants underline their importance in modern surgical practices. The incorporation of individualized solutions ultimately enhances patient outcomes and fosters a smoother surgical journey.
Material Matters: Engineering Implants for Optimal Performance
The choice of material for 3D printed implants is crucial:
- Biocompatible Materials: Materials like titanium offer excellent strength, durability, and biocompatibility, making them ideal for load-bearing implants like knee and hip replacements.
- Advanced Materials Research: Development of new materials with improved properties like enhanced bone osseointegration (fusion with bone) is ongoing.
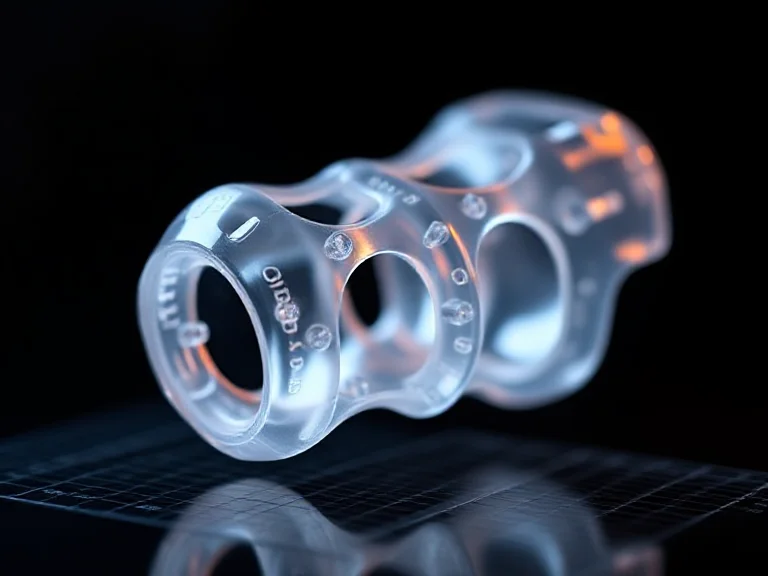
Materials Used in 3D Printing of Implants
The advancement of 3D printing technology has significantly broadened the range of materials available for the fabrication of customized implants. One of the most critical factors in material selection is biocompatibility, which ensures that the implant can interact safely with the human body without eliciting an adverse reaction. Biocompatible metals, such as titanium and its alloys, are widely employed due to their strength, durability, and excellent fatigue resistance. These metals also have an affinity for osseointegration, allowing them to bond effectively with bone tissue, which enhances the overall stability of the implant.
Another category of materials includes polymers, which offer lower density and can be tailored to exhibit specific mechanical properties. Commonly used polymers in 3D printed implants include polyether ether ketone (PEEK) and polylactic acid (PLA). PEEK, in particular, is favored for its high tensile strength and resistance to wear, making it suitable for load-bearing applications. Meanwhile, PLA is biodegradable, serving as an attractive option for temporary implants intended for eventual absorption by the body, reducing the need for surgical removal.
Cranial and facial surgeries also benefit immensely from customized 3D printed implants. Surgeons can now use 3D printing technology to produce patient-specific cranial plates and facial reconstruction implants.
The applications of customized 3D printed implants extend beyond mere repair; they offer a glimpse into the future of personalized medicine where treatments are not just effective but also align closely with patient-specific requirements.
Ceramics represent another essential material class in 3D printing of implants due to their favorable properties, including biocompatibility and aesthetic appeal. Bioceramics, such as hydroxyapatite, mimic the mineral component of bone and promote bone growth, thus enhancing implant integration. The unique characteristics of ceramics make them ideal for applications in orthopedic and dental implants.
3D printing technology is revolutionizing the field of implantology by enabling the creation of customized 3D printed implants. These innovative implants offer patients a perfect fit, improved functionality, faster recovery times, and a brighter future in healthcare.
Ultimately, the choice of material for 3D printed implants can profoundly affect their performance and safety. Factors such as mechanical strength, wear resistance, and the ability to integrate with surrounding tissue are paramount when determining the ideal material for specific medical applications.
A Brighter Future for Patients: Beyond Traditional Implants
The potential of 3D printed implants extends beyond current applications:
- Complex Reconstructive Surgery: 3D printing allows for the creation of intricate facial implants for patients with severe injuries or birth defects.
- Bioprinting Integration: Researchers are exploring the use of bioprinting to create implants with living cells and tissues, potentially leading to even better integration with the body and reduced risk of rejection.
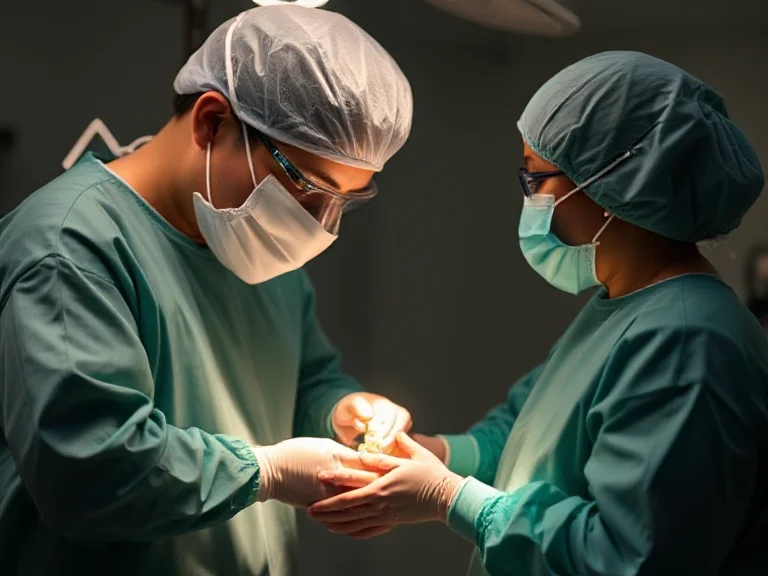
Applications of Customized Implants in Medicine
The shift towards personalized medicine is not just a trend; it reflects a growing understanding of patient needs. The experiences of individuals utilizing customized 3D printed implants illustrate significant advancements in orthopedic and reconstructive surgery.
In summary, as the technology behind customized 3D printed implants advances, it not only shifts the cost landscape but also presents a promising route toward improved accessibility for patients globally.
Customized 3D printed implants are revolutionizing various fields within medicine, providing unique solutions tailored to individual patient needs. The versatility of these implants has significantly impacted orthopedic procedures, dentistry, cranial and facial surgery, and even organ transplants. One of the most prominent applications is in orthopedics, where implants such as joint replacements and bone plates are designed to conform perfectly to a patient’s anatomical structure. For instance, a recent case study highlighted the successful use of a 3D printed ankle implant that reduced recovery time and improved mobility compared to traditional treatments.
In the dental field, customized implants have transformed restorative procedures. Dentists can now create personalized dental implants that fit seamlessly into the patient’s mouth, enhancing comfort and aesthetics. A notable example includes the implementation of 3D printed dental crowns and bridges, which significantly shorten the time taken for fabrication while delivering superior fit and function.
Cranial and facial surgeries also benefit immensely from customized implants. Surgeons can now use 3D printing technology to produce patient-specific cranial plates and facial reconstruction implants. A striking case involved a patient with severe facial deformities who received a 3D printed implant, resulting in enhanced facial symmetry and improved quality of life. Furthermore, in the area of organ transplantation, early-stage experiments with scaffolds made by 3D printing have shown promise in generating bio-compatible structures that could potentially lead to the replacement of failing organs.
The applications of customized 3D printed implants extend beyond mere repair; they offer a glimpse into the future of personalized medicine where treatments are not just effective, but also align closely with patient-specific requirements. The flexibility and advancements in this technology will continue to redefine surgical practices across various specialties.
Perfect Fit for a Perfect Recovery
3D printing technology is revolutionizing the field of implantology by enabling the creation of customized solutions. These innovative implants offer patients a perfect fit, improved functionality, faster recovery times, and a brighter future in healthcare.
Patient Perspectives: Stories and Experiences
Stories from patients who have undergone procedures with customized 3D printed implants often reveal a transformative experience. For many, the journey begins with a diagnosis that can be overwhelming, prompting a search for solutions that are both effective and accommodating to their unique anatomical needs. One patient recalls the moment they learned about 3D printed implants; “I felt a glimmer of hope knowing there was a tailored solution that could address my specific condition,” they stated. This sentiment echoes across numerous testimonials.
The process of receiving a customized implant not only addresses physical concerns but also significantly impacts emotional well-being. Many patients report feeling more in control of their health outcomes when engaging in discussions about the design and functionality of their implants. A particular individual shared their experience: “Being part of the decision-making process empowered me. I felt like I was not just another number, but my particular needs were being considered.” This sense of collaboration with healthcare professionals contributes to a more positive treatment experience.
After surgery, patients often express relief and satisfaction with the results of their unique implants. This sentiment is captured in a testimonial from a patient who underwent hip replacement surgery: “With my custom implant, I can once again participate in activities I thought I would never enjoy again, like hiking and playing with my grandchildren. The difference is truly life-changing.” Recovery stories not only highlight the physical benefits but also underline the emotional victories that accompany them. The joy of regaining mobility or overcoming pain is a common thread in their narratives.
The shift towards personalized medicine is not just a trend; it reflects a growing understanding of patient needs. The experiences of individuals utilizing customized 3D printed implants illustrate significant advancements in orthopedic and reconstructive surgery. These innovations pave the way for a future in which every patient receives care tailored to their distinct circumstances, fostering a sense of hope and renewal in their lives.
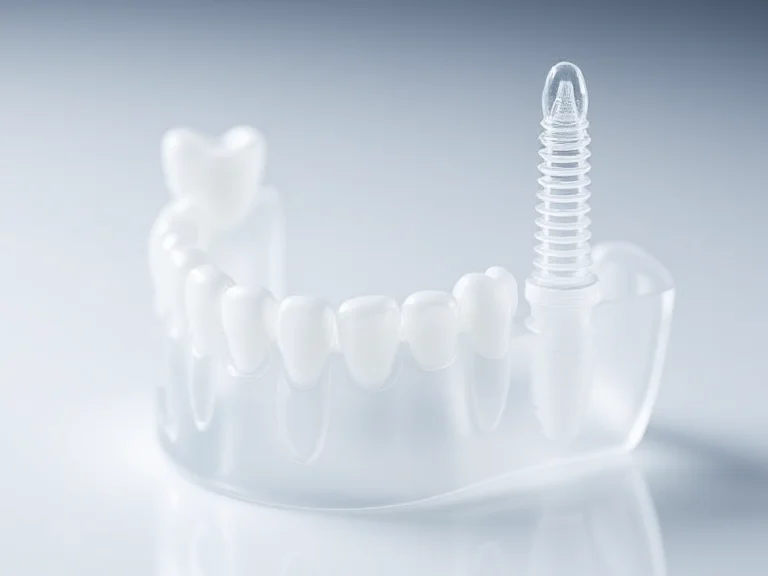
Cost Implications and Accessibility
The burgeoning field of customized 3D printed implants has introduced a progressive approach to medical solutions, particularly in orthopedics and dental applications. One of the most significant aspects to consider is the cost implications compared to conventional implants. Traditional implants often incur high costs due to extensive manufacturing processes, which include multiple middlemen in the supply chain, from design to production and distribution. In contrast, 3D printed implants streamline this process significantly, reducing overhead costs and eliminating many intermediaries. As a result, patients may find 3D printed alternatives to be a more economical option.
Several factors come into play when considering the pricing of these customized implants. The complexity of the design, the materials used, and the individual requirements of the patient can all affect the final cost. Furthermore, the geographic location and the healthcare provider’s policies may result in significant variations in pricing. For example, regions with advanced manufacturing technologies and better access to 3D printing capabilities may offer lower prices compared to less developed areas. Additionally, as the technology continues to evolve, further advancements could drive down costs, making these customized solutions more accessible to a broader range of patients.
From the perspective of the healthcare system, investing in 3D printing technology could potentially lead to long-term savings. With more precise fits and the possibility of reduced surgical complications, healthcare providers may experience a decrease in post-operative care costs. As the integration of 3D printing into standard medical practices becomes more prevalent, it could open doors to insurance coverage for personalized implants, extending accessibility to those who may currently be unable to afford such options.
In summary, as the technology behind customized 3D printed implants advances, it not only shifts the cost landscape but also presents a promising route toward improved accessibility for patients globally. The convergence of innovation, changing healthcare policies, and the pursuit of affordability will likely redefine the implant market in the coming years.
Regulatory Challenges and Standards in 3D Printing
The rise of 3D printing technology in the medical field has prompted significant regulatory considerations regarding its application in producing customized implants. One of the primary challenges faced by manufacturers involves navigating the complex landscape of regulations, which differs greatly across jurisdictions. Regulatory bodies such as the U.S. Food and Drug Administration (FDA) and the European Medicines Agency (EMA) have established distinct frameworks to ensure that 3D printed implants meet safety and quality standards. However, these frameworks can be sometimes slow to adapt to the rapid advancements in 3D printing technology.
Manufacturers of 3D printed implants are required to provide extensive documentation that demonstrates compliance with strict safety protocols. This includes validating the materials used in production, the printing processes, and the final product’s performance, leading to an arduous certification process. As each device may be customized to the specific anatomical requirements of a patient, the regulatory bodies often necessitate thorough pre-market approvals, which can lead to delays in bringing innovative solutions to market.
Additionally, once a product has received approval, ongoing monitoring is essential to ensure its continued safety and efficacy. Post-market surveillance includes tracking the performance of 3D printed implants in real-world applications, highlighting the critical need for data collection and analysis. Manufacturers must establish robust reporting mechanisms to capture any adverse events or complications that may arise. This not only ensures compliance with regulatory expectations but also reinforces the commitment to patient safety in the face of emerging technologies.
Without doubt, the path for manufacturers to achieve regulatory compliance in the realm of 3D printed implants is challenging. However, striking a balance between innovation and rigorous safety standards is crucial for fostering public trust and ensuring optimal patient outcomes. The continuous evolution of regulatory frameworks will play a vital role in determining the future landscape of custom 3D printed implants.
The Future of Customized 3D Printed Implants
As technology continues to evolve, the future of customized 3D printed implants holds significant promise for the healthcare industry. Anticipated advancements in 3D printing technologies will enhance the precision and effectiveness of implants, leading to improved patient outcomes. Emerging materials, such as biocompatible polymers and advanced metal alloys, are already being researched to provide even more customized solutions that cater to the unique anatomical needs of patients. These materials not only enable greater customization but also enhance the integration of implants with existing biological tissues.
Moreover, the integration of artificial intelligence (AI) and machine learning is expected to revolutionize the customization process. These technologies can analyze vast amounts of data from patient scans to create highly accurate, bespoke implant designs. By incorporating real-time analytics, surgeons and medical professionals can optimize implant specifications, making informed decisions that contribute to better surgical outcomes. AI may also facilitate predictive modeling, allowing for the simulation of surgical procedures before they take place, minimizing risks associated with complex operations.
Furthermore, the ongoing collaboration between biomedical engineers and healthcare professionals is essential for creating robust frameworks that ensure the safe use of 3D printed implants. Regulatory advancements will play a crucial role in shaping the future, ensuring that these novel implants meet stringent standards for safety and efficacy. Such frameworks will pave the way for broader adoption within surgical practices, enabling healthcare providers to deliver patient-centered care that is both efficient and tailored to individual needs.
In light of these advancements, it is clear that the intersection of technology and patient care will redefine the landscape of medical implants. Continuous innovation in 3D printing technology, coupled with enhanced materials and intelligent systems, positions customized implants as a leading solution in the pursuit of improved surgical practices and overall patient health.
Looking to learn more about customized 3D printed implants?
Search for terms like “3D printed knee replacements for better fit” or “benefits of bioprinted implants” to delve deeper into this groundbreaking technology.